Improving Efficiency in Industrial Applications
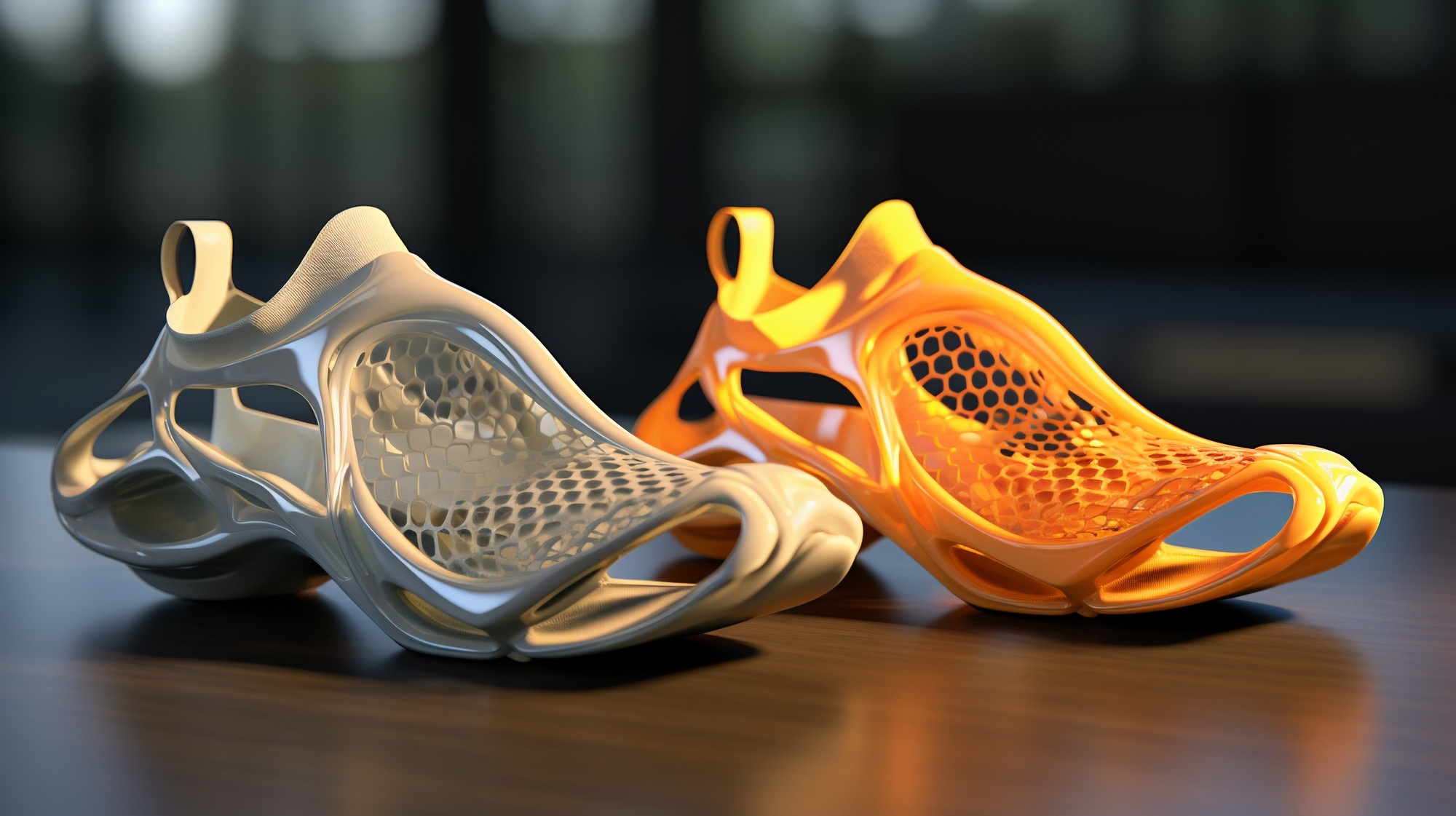
In today’s competitive world, industries are always looking for ways to increase efficiency, reduce costs, and improve productivity. Innovative materials and smart technologies are helping drive these efficiency gains across many sectors. Here are some key areas:
Lightweight Yet Strong Materials
Using lighter but stronger materials is one of the most effective ways to boost industrial efficiency because lighter components require less energy to power, move, or transport.
This is where advanced composite materials really shine. Industrial composites made from resins reinforced with fibers like carbon, glass or aramid offer incredible strength-to-weight ratios compared to metals.
For example, fiber-reinforced polymer (FRP) composites can be 5 times stronger than steel at only a quarter of the weight. This weight savings results in reduced energy consumption for applications like pump impellers, tanks, pipes, and pressure vessels.
Durable, Low Maintenance Materials
Besides being lightweight and strong, many composites also offer excellent durability, corrosion resistance, and require very little maintenance. This reduces downtime and operating costs over decades of use.
Fiberglass reinforced plastics (FRP) are a perfect example used across many harsh industrial environments. FRP tanks, scrubbers and pipe systems are impervious to chemical attacks and require almost no maintenance beyond basic inspections.
The superior fatigue resistance of carbon fiber composites makes them ideal for items that experience cyclic stresses and vibrations, like machine components, bearings, or drivetrains.
The experts at Aerodine Composites say that with little to no painting, plating or anti-corrosion coatings needed, industrial composites pay back their slightly higher upfront costs many times over their long service lifetimes.
Precision Manufacturing and Automation
Advanced manufacturing techniques and automation are driving efficiency in production lines and factories. Computer-controlled processes ensure exceptional quality control and uniform output.
For composites, automation enables precise control over reinforcement layups, consolidation pressures, and curing cycles. This optimizes material properties and minimizes variances between parts.
Automated systems can produce complex composite shapes that would be extremely difficult or impossible with traditional metalworking. Examples include seamless curved ducts, pressurized cylinders, and large one-piece components.
Robotic systems and computer numerically controlled (CNC) machining also boost throughput by producing parts faster with tighter tolerances than manual labor.
Reducing Maintenance and Downtime
Minimizing maintenance requirements and associated downtimes is a key focus area for improving industrial efficiency. Here too, composites deliver enormous advantages over traditional materials.
The inherent corrosion resistance of FRP composites means pipes, tanks and vessels avoid the perpetual need to sandblast and repaint metal surfaces. The elimination of hazardous coating removal and reapplication every few years cuts down on costs.
FRP components also resist buildup of scale, deposits and biological growth that often plague metallic systems in harsh environments. The need for cleaning is significantly reduced.
Compared to metals prone to cracking, fatigue, and corrosion, composites significantly extend the service intervals with no gradual deterioration or weakening over time.
Efficient Design Flexibility
One of composites’ most useful attributes is their ability to consolidate multiple components into an integrated, unified design. This provides space and weight savings while enhancing efficiency.
For instance, composite transmission casings, brackets and bearing housings can all be combined into a single, seamless unit that optimizes load transfers and eliminates joints prone to failure.
Integrated FRP plenums provide a lightweight, compact enclosure for industrial air handling units by combining the structural housing, internal baffling, and attachment points.
Complex process equipment can leverage composite’s design flexibility to incorporate molded-in insulation, serviceability features, and eliminate secondary fixtures.
Conclusion
The future for industrial applications is clearly focused on efficiency gains through new manufacturing methods, smart automation, reducing energy intensities, and leveraging multifunctional, low maintenance materials. Advanced composites stand poised to play a pivotal role in all areas as the drive for optimization continues.